Physics, mechanical engineering, and economics with the Truetrac
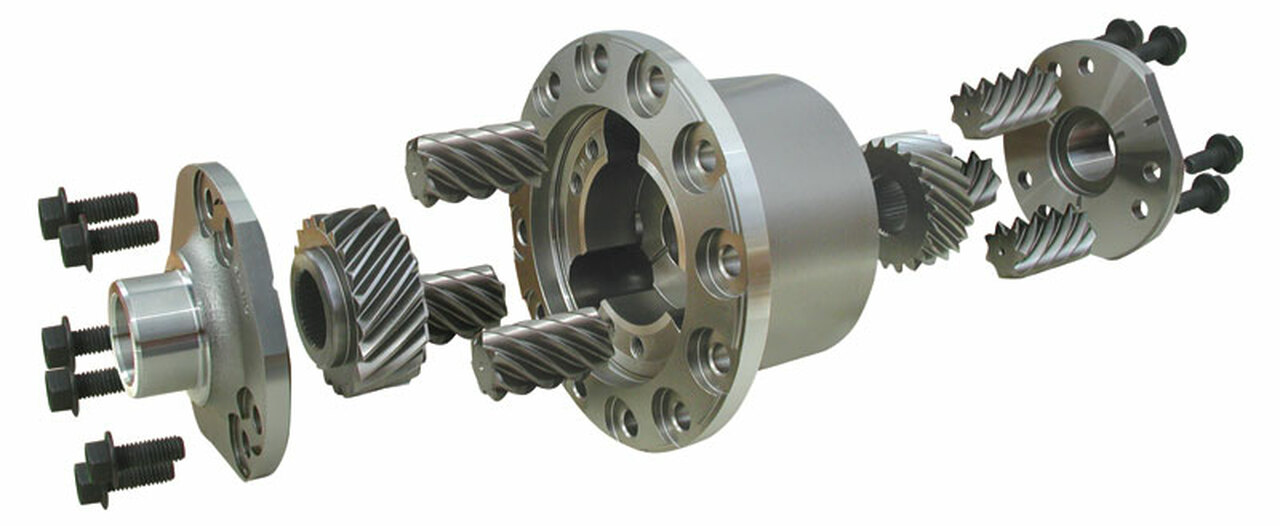
Part of the job of home schooling kids is to get them to work with their hands and to learn the mechanics of things. Enter a 1997 S10 4 cylinder with a 10 bolt rear end.
It didn’t need an LSD (limited slip differential) except for those 1 percent of times it’s raining, roads are slick, I’m gassing it, and not moving. The Truetrac was on sale (relatively) and it was a good excuse to add an LSD and teach the kids a thing or two.
1 Eaton Truetrac 912A317 $502.02
2 ACDELCO 8660S axle seals $7.06
2 TIMKEN LM501349 bearing, TIMKEN LM501314 race cup $50.53
1 Fel-Pro RDS55072 cover gasket $6.18
2 quarts Valvoline full synthetic 75w90 $25.34
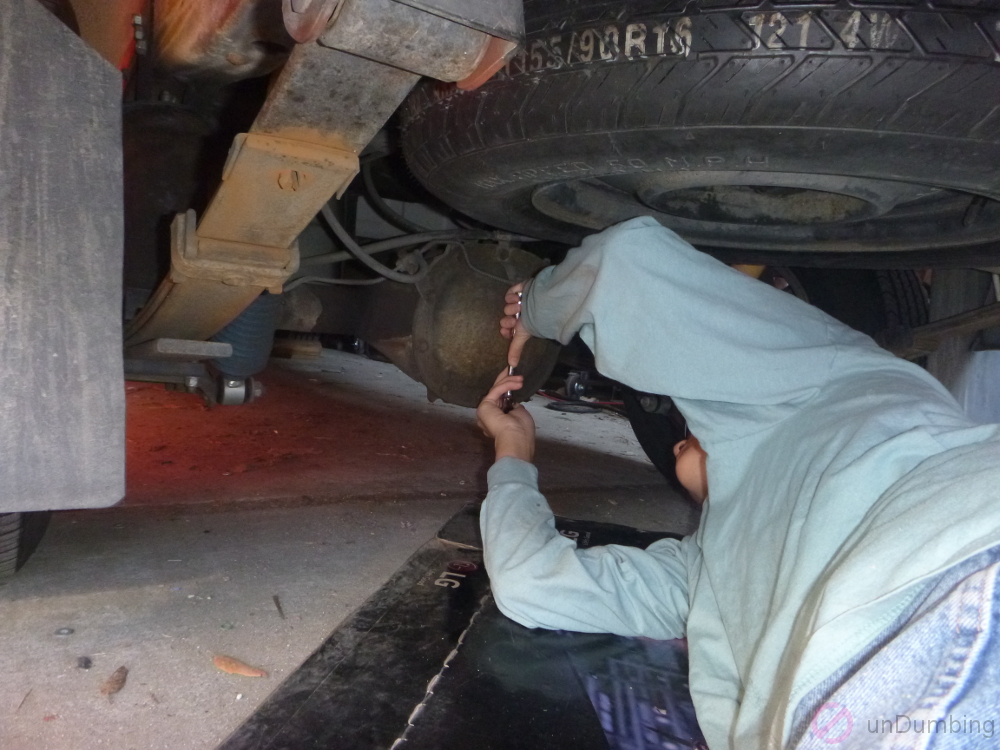
My older kid noticed that metric sockets did not fit snugly on the cover bolts, but standard sockets did, even though I told him to use metric sockets. As we continued disassembling the axle, we realized that the entire truck was metric, except for the axle.
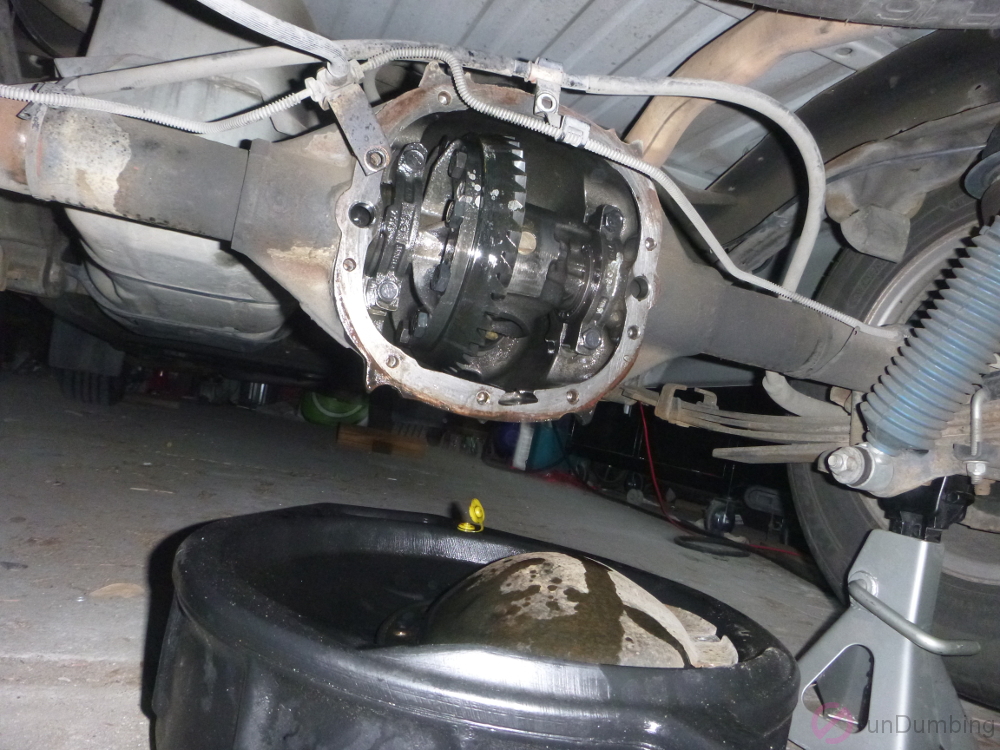
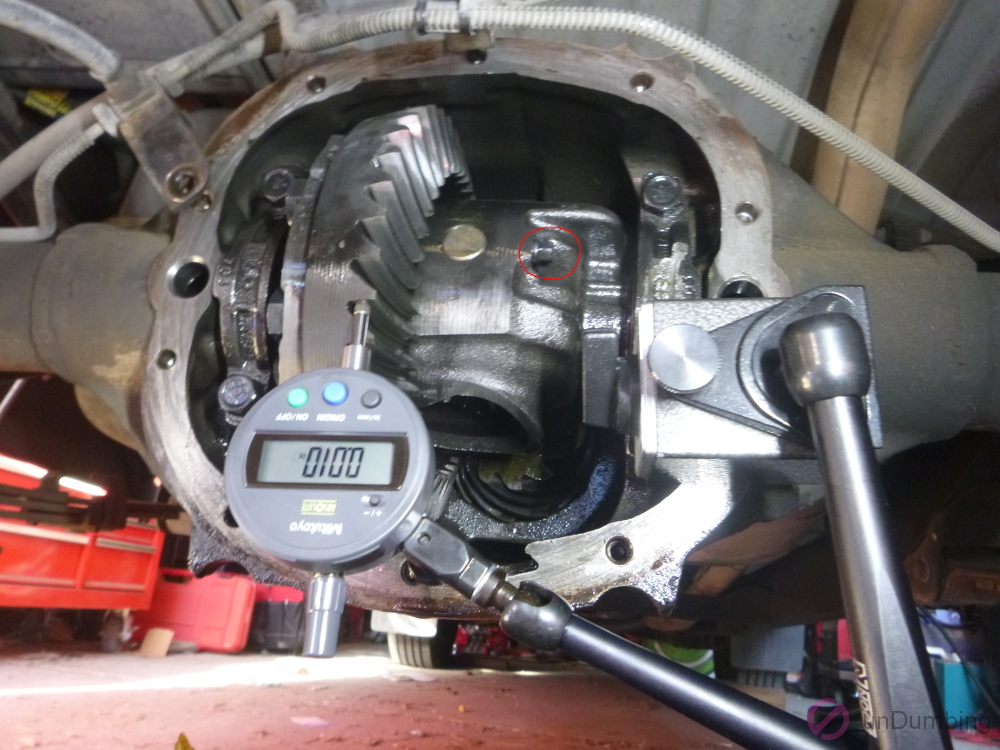
After adding some heat to the bolt area (red circle) with a propane torch, the bolt came off easily. Luckily I didn’t force it without heat, otherwise, the job would’ve taken longer. GM spec for backlash is 6 (0.006″) – 10 (0.010″) mils.
Before removing the center pin that supported the pinion gears in the differential, we studied the operation of the differential by mimicking left and right turns, by having one wheel stationary and the other spinning. They saw with their own eyes what the gears (side and pinion) were doing inside an open differential. I made sure they understood the operation before moving on.
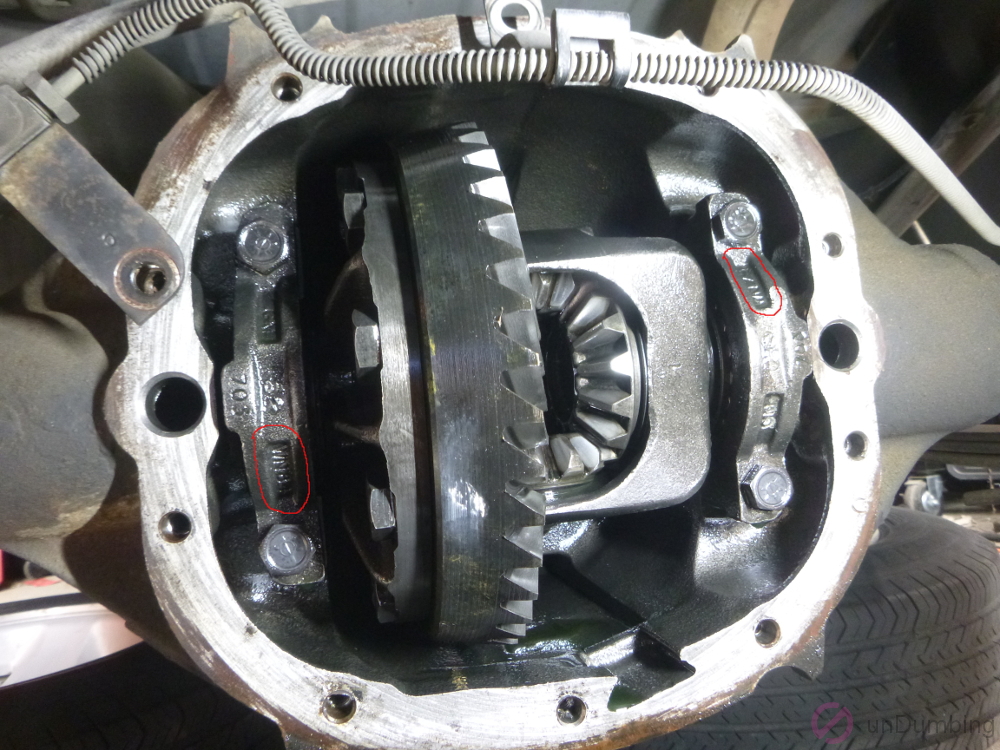
For the rest of the install, I got involved with theory, naming conventions, operations, etc. with the boys that I neglected to take pictures. Oh well. Guess I have to be better next time.
We removed the differential from the carrier and made comparison measurements with the Truetrac. There were very little differences, as expected, but I wanted to make sure. This Truetrac was made in Taiwan.
The ring gear bolts (reverse thread) were removed (by both kids), inspected for thread galling, and reused with the
stock ring gear (4:10) on the Truetrac. The bolts were torqued to 65ft lbs in a circular pattern (not criss-cross). I held a long pry bar while the kids torqued the bolts using a long torque wrench.
I found two leather strips (2″ x 0.5″) included in the Truetrac box and was confused at why they were in there. At least for us, they were taped to the surfaces of the pry bar against the Truetrac to avoid marring the surface. Good on Eaton for including these strips, if they were actually for this purpose.
After attaching the ring gear, we installed new differential bearings onto the Truetrac. The stock bearing race cups were worn and it was good that we purchased new bearings and cups.
During the removal of the stock differential, I found two thick bearing spacers on each side. The thicknesses looked the same, but using calipers we netted a 236 mils (0.236″) spacer for the left and a 245 mils (0.245″) spacer for the right. The Truetrac was installed into the carrier with backlash at 10 mils (0.010″) like the oem differential. The bearing caps were torqued to 60ft lbs.
One of the long discussions I had with the boys was whether we should replace the oem axles with new ones. New axles, from Dutchman, were $310 for a pair with material that was harder than oem. There were cheaper options, but I wanted Made in USA and to support a small business.
I inspected the oem axles and while they had some dimples near the axle bearing area, GM gave a pass on these axles. I explained to the boys that even though the axles could look troubling, these axle was considered (maybe) 90% or passable by GM and it avoided the scrap heap. Besides, the axles did feel good installed (before removal). It didn’t feel like it had abnormal wear when radially tested.
We also discussed the risks and rewards over reusing 147k-mile axles vs new ones. They summed up that $310 for new axles that were almost 20% of the value of the S10 didn’t make any sense. I inspected the bearings and axles and to me they were passable. I wanted new axles, but (we) decided to reuse the axles, axle bearings, but replace the seals as the practical reason.
The Truetrac install lasted three weekends. In between weekends we watched animated videos on the operation of a Truetrac. I explained the semi-lockup characteristics of the internal worm gears that wanted to separate and jam themselves against the differential carrier. While different from an LSD with clutches, the principles of internal differential gears wanting to separate and jam themselves against the carrier were similar, but this time against friction material which doesn’t last the lifetime.
While the S10 didn’t really need an LSD like a Truetrac, the boys had a lesson in physics, mechanical engineering, and economics. I really wanted new axles😢, but it was ultimately their decision on the cost basis of new axles. I hope they made the right decision. 😉